Delays are, unfortunately, a common occurrence in construction projects and are often associated with significant cost impacts. When delays are caused by the client or principal and extend the project’s completion date, the contractor may be entitled to recover prolongation costs — the additional time-related expenses incurred due to remaining on site longer than originally planned.
These costs are distinct from disruption claims or liquidated damages, and typically arise when an Extension of Time (EOT) is granted. Yet, despite being frequently referenced in negotiations and disputes, prolongation costs are often misunderstood — both in terms of what they cover and how they should be assessed.
This article explores the concept in detail, including how prolongation claims arise, how they differ from other delay-related entitlements, and provides a brief overview of how they can be quantified.
What are prolongation costs?
Prolongation costs refer to the additional expenses a contractor incurs when a construction project takes longer to complete than originally planned, due to delays caused by the client (or principal) or circumstances beyond the contractor’s control.
These delays may result from unforeseen latent conditions (such as hidden defects, utilities issues, or soil contamination) or external factors like supply chain disruptions caused by events such as the COVID-19 pandemic. Under the terms of most modern construction contracts, the contractor is typically entitled to recover these time-related costs for remaining on site longer than initially anticipated.
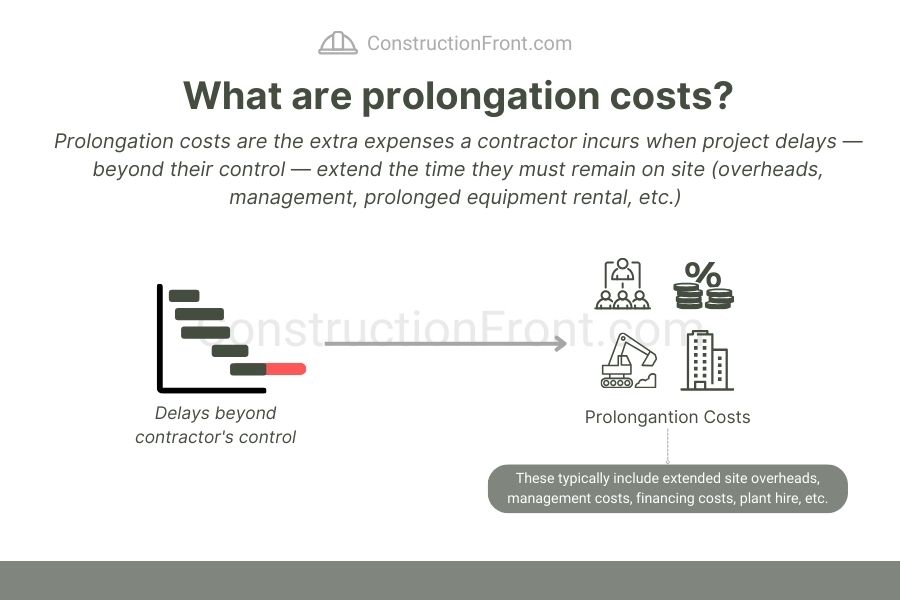
Typical examples of prolongation costs include, but are not limited to:
Prolongation Costs | Examples |
Site Overheads | Site management salaries, plant hire, utilities, insurance, accommodation costs |
Head Office Overheads | Administrative salaries, office-related costs |
Financing Costs | Interest on loans or financial charges incurred due to delays |
Example of Prolongation in Construction Projects
A common example of prolongation costs occurs when contractors encounter latent conditions on site, such as buried utilities, archaeological artifacts, or contamination, discovered during excavation. These issues can take weeks, months, or even years to resolve, causing significant program delays and financial strain on the contractor, who could not have predicted or priced these risks during the bidding phase.
Real World Examples:
- Sydney Light Rail Project (Australia) – During the construction of Sydney’s Light Rail network, contractors encountered contaminated soil and unmapped utilities. The discovery of contaminated ground required extensive testing and remediation, causing several months of delays. The project’s timeline was also affected by the need to divert utilities that were not originally documented. These unforeseen issues led to prolongation costs as contractors had to extend their time on-site to manage the delays, requiring additional resources and time. (More on Sydney’s troubled $2.1bn light rail project delayed again)
- Boston’s Big Dig (USA) – During the construction of Boston’s Central Artery/Tunnel Project (commonly known as the “Big Dig”), contractors faced numerous delays due to buried utilities and contaminated soil. The discovery of underground oil tanks and hazardous materials led to prolonged excavation work and forced the project to extend beyond its original completion date. These issues added significant costs to the project, which were primarily driven by the extended timelines and the need to address the unforeseen contamination. (More on: The Big Dig: Learning from a Mega Project)
- Crossrail Project (London, UK) – During the construction of Crossrail, London’s underground rail network, contractors encountered buried utilities and contaminated ground. The discovery of hazardous materials and uncharted infrastructure led to significant delays and extended the timeline. These unforeseen conditions caused prolongation costs as additional time and resources were required for remediation and to reroute utilities. More on: Crossrail delay: The report | London City Hall
What is a Prolongation Claim?
A prolongation claim is a formal request submitted by a contractor to recover the additional costs of staying on site longer than originally planned, following a delay that was not their fault. These claims typically arise when an Extension of Time (EOT) is granted for delays caused by the client, principal, or events beyond the contractor’s control.
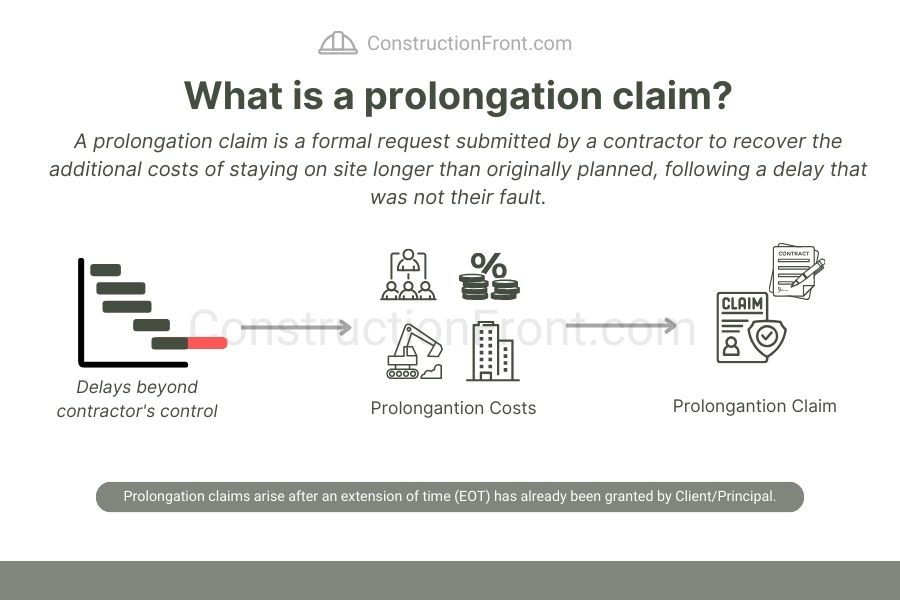
It is important to note that while an EOT gives relief from liquidated damages, it doesn’t automatically entitle the contractor to cost recovery. To claim prolongation costs, the contractor must go a step further — they must prove that the delay impacted the critical path of the program and that the additional costs were a direct result of that delay.
Prolongation claims differ from disruption or acceleration claims in that they focus solely on time-related costs. These may include extended site overheads, head office allocations, and financing costs — all of which must be supported by proper documentation. Typically, the strength of a prolongation claim depends on well-maintained cost records, program updates, and evidence showing that reasonable steps were taken to mitigate the delay’s impact.
How to Calculate Prolongation Costs?
Calculating prolongation costs involves demonstrating the financial impact of a delay on the contractor’s operations. The process begins with establishing that the delay affected the project’s critical path — meaning it directly contributed to an extension of the overall completion date. Once this link is proven, the following cost categories are typically considered:
Site Overheads: These include project-specific expenses that continue throughout the delay period, such as site management salaries, temporary facilities, utilities, security, and plant or equipment hire.
Head Office Overheads: Indirect costs from the contractor’s corporate operations, which are often apportioned to the delayed project using formulas such as the Emden or Hudson method.
Financing Costs: Interest on loans or extended working capital needed to support ongoing operations during the delay.
Other Direct Costs: These may include additional insurance premiums, accommodation, demurrage, or extended warranties tied to the delayed duration.
The most common methods used to quantify these costs are:
Actual Cost Method: Based on verifiable expenses during the extended period, supported by project accounting records.
Formula-Based Methods: Such as the Hudson, Emden, or Eichleay formulae, generally used for head office overhead recovery.
Preliminaries Rate Method: Applying daily or weekly rates from the contract preliminaries for ongoing site costs (typically, explicitly detailed under the construction agreement).
Regardless of the method used, the contractor must ensure the figures are evidence-based, consistent with the contract, and reflective of the true additional burden of staying on site longer.
The Hudson Formula
The Hudson Formula is a widely used method for calculating prolongation costs due to project delays. It helps quantify time-related costs, such as site overheads, plant hire, insurance, and accommodation, when delays extend the project timeline.
The formula is as follows:
Prolongation Cost= (Total Project Overheads / Original Duration) × Delay Period
Where:
Total Site/Project Overheads refers to all costs incurred on-site (e.g., management, machinery, utilities).
Original Duration is the initially agreed project timeline.
Delay Period is the period the contractor remains on site due to delays.
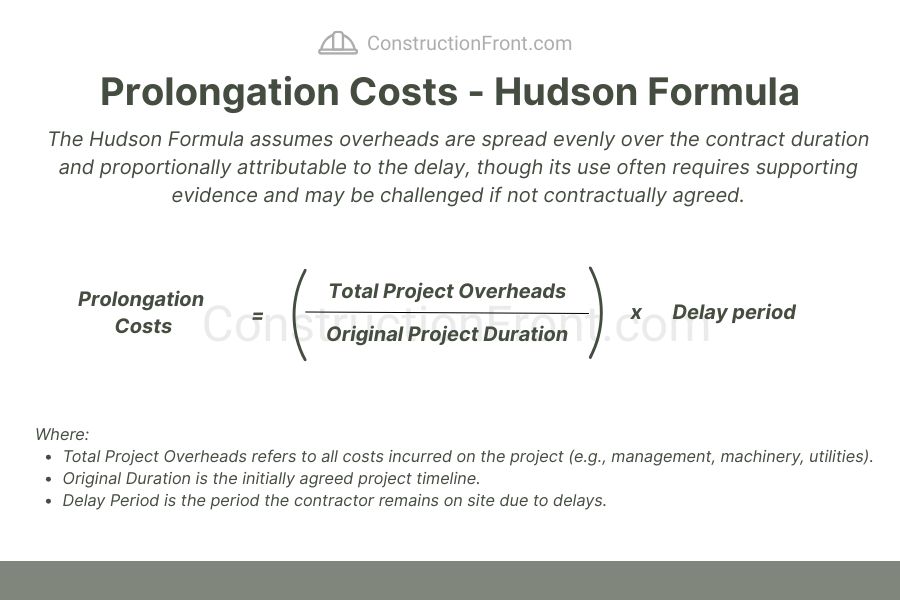
This formula allows contractors to claim a fair portion of the overheads based on the extended project duration, provided they can substantiate the delay was outside their control. Proper documentation, such as updated project timelines and cost records, is essential to support the claim.
Submitting a Prolongation Claim
Once prolongation costs have been calculated, pursuing a successful claim involves demonstrating entitlement, causation, and quantum — typically through structured documentation and contract-compliant processes. Key steps include:
Notify the Delay Promptly: Follow the contract’s notice provisions, such as early warning notices or notice of delays, to inform the principal of the delay event as soon as it occurs.
Secure an Extension of Time (EOT): Ensure the delay has been formally acknowledged and an EOT has been granted. Without this, there is no basis for claiming prolongation costs.
Prepare the Claim in Full: Structure the variation claim clearly, typically following the SCL (Society of Construction Law) Protocol framework:
Cause: Describe the event and how it arose.
Effect: Demonstrate the impact on the critical path and project completion.
Entitlement: Refer to the relevant contractual clause.
Substantiation: Provide detailed evidence to support the cost claim.
Support with Contemporaneous Records: Include updated programs, site diaries, cost reports, resource logs, and correspondence that demonstrate both the delay and the associated expenses.
Show Mitigation Measures: Detail any reasonable steps taken to reduce or avoid the delay’s impact — a critical factor in the principal’s assessment of the claim.
A well-prepared prolongation claim is not just a matter of entitlement — it is about telling a clear, credible story backed by records, aligned with the contract, and grounded in accurate cost data.
FAQ - Prolongation Costs and Claims
Prolongation vs EOT vs Disruption Costs / Claims
To better understand how prolongation cost and claims fit within the broader context of construction delay entitlements, it helps to distinguish them from disruption and Extension of Time (EOT) claim:
Category | Extension of Time (EOT) | Disruption | Prolongation |
Definition | Additional time granted to complete the project due to delays beyond the contractor’s control | Loss of productivity or efficiency in executing the works | Additional costs incurred from remaining on site longer due to delays |
Entitlement | Provides relief from liquidated damages, but not automatically from cost recovery | Entitles the contractor to recover costs arising from inefficiencies | Entitles the contractor to recover time-related costs associated with extended site presence |
Cause | Delays caused by the principal or external events | Disruption in planned sequence of work or inefficient working due to interference or late access | Delays caused by events beyond the contractor’s control, often following an EOT |
Focus | Time | Productivity | Cost |
Acceleration Claim vs Prolongation Claim
An acceleration claim arises when a contractor is required to speed up the work to recover lost time due to delays. This typically involves additional costs, such as overtime or extra resources, to meet the original deadline.
A prolongation claim, on the other hand, seeks compensation for the additional time-related costs incurred when the project is delayed beyond the original schedule, typically due to factors outside the contractor’s control. This covers extended overheads, financing costs, and other time-based expenses.
In short, acceleration claims are for speeding up the project, while prolongation claims are for the costs of extended project duration.
Need Help with Prolongation Costs and Claims?
Do not hesitate to contact us (click here) for specialised advice in the construction industry.
Sources
- DELAY AND DISRUPTION PROTOCOL by the Society of Construction Law (SoCLA) – 2nd_Edition_Final
- The Big Dig: Learning from a Mega Project | APPEL Knowledge Services
- Crossrail delay: The report | London City Hall
- The two Hudson Formulas
- Assessing Loss and Expenses Claim by Prolongation Cost
- The Hudson Formula SCL Paper 230.pdf
Disclaimer: The articles on this blog are for informational and educational purposes only and do not constitute legal advice. While we strive to provide accurate and up-to-date information on construction law, regulations may vary by jurisdiction, and legal interpretations can change over time.